Czy MES może zapewnić dane o statusie realizacji produkcji bez bezpośredniego podłączenia do parku maszynowego ?
Każdej firmie produkcyjnej zależy na posiadaniu informacji o postępach prac – to fakt. Przecież właśnie dzięki aktualnym danym można reagować na nieprawidłowości w procesie produkcyjnym.
Klasyczne systemy MES pozwalają na zbieranie takich informacji na dwa sposoby:
pobieranie danych ze sterowników PLC bezpośrednio z maszyn (w przypadku braku sterowników PLC można się pokusić o podłączenie innych mierników np. zużycia prądu – brak zużycia prądu oznacza przestój, pobór prądu oznacza wykorzystanie maszyn)
raportowanie rozpoczęcia i realizacji prac poprzez stacje raportujące na hali produkcyjnej (np. stanowiska komputerowe z czytnikami kodów kreskowych, przenośne terminale kodów kreskowych, tablety).
Okazuje się, że pobieranie danych bezpośrednio z maszyn to domena pewnych firm, branż, a nie standard. Wszystko zależy od profilu produkcji i potencjalnych korzyści.
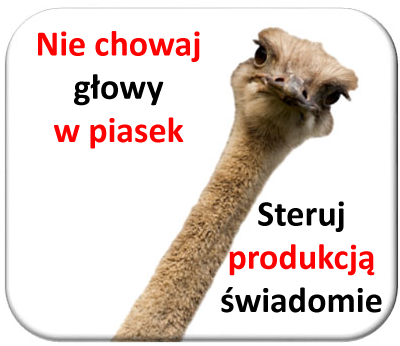
Największe korzyści wynikające z podłączenia się bezpośrednio do maszyn uzyskamy przy produkcji wielkoseryjnej. W firmach, które posiadają wyśrubowany wskaźnik OEE, nawet 10% zwiększenie mocy produkcyjnych może być warte inwestowania w podłączenie maszyn do systemów MES. Jest to często także wymóg w firmach gdzie krytyczna jest kontrola odchyleń od norm jakościowych w celu zachowania powtarzalności jakości serii produkcyjnych , jak to jest np. w branży motoryzacyjnej.
W przypadku produkcji jednostkowej, czy niskoseryjnej mierzenie i optymalizacja wykorzystania maszyn ogranicza się zazwyczaj wyłącznie do tych stanowiących „wąskie gardła”.
A jak zmierzyć postępy prac i wykorzystanie mocy produkcyjnych w produkcji „ręcznej”, czyli tam, gdzie wąskimi gardłami są głównie ludzkie możliwości manualne. Nie ma w końcu do czego się podłączyć.
Z doświadczenia wynikającego z wdrożeń rozwiązania L-Systems MES możemy stwierdzić, iż najbardziej rozpowszechnionym i zapewniającym najlepsze przełożenie (mierzone czasem wdrożenia, kosztem oraz uzyskanym efektem) są stanowiska raportujące pozwalające na szybkie, a co za tym idzie nisko kosztowe raportowanie operacji z wykorzystaniem kodów kreskowych reprezentujących np. pracownika, zlecenie produkcyjne, produkt, operację itp. Istotne znaczenie ma także optymalizacja interfejsu systemu pod kątem ergonomii pracy, innymi słowy użytkownik powinien mieć dostępne „pod ręką” wyłącznie używane przez niego funkcje i nic ponadto. Rejestracja on-line czasu pracy, jego typu, a także przestojów oraz ich przyczyn przekłada się wprost na przeliczanie czasu pracy i wskaźnika wykorzystania maszyn (OEE).
Ktoś zada pytanie, a gdzie tutaj jest miejsce na optymalizację planowania mającą na celu zwiększenie produktywności (wskaźnik OEE) ? Jakie funkcje i jakie narzędzia w tym zakresie mogą zaoferować systemy klasy MES wyposażonych w funkcje planistyczne ? Odwołując się do naszych doświadczeń wynikających z wdrożeń systemu L-Systems MES możemy stwierdzić, iż stosowanie rozwiązań standardowych lub próby w tym kierunku zmierzające zwykle kończą się porażką lub kompromisem pomiędzy rzeczywistymi potrzebami przedsiębiorstwa, a standardowymi możliwościami systemu (jak wiadomo kompromis uważa się za porażkę wszystkich na niego przystających, nikt do końca nie jest zadowolony). Optymalne planowanie to planowanie w pełni uwzględniające specyfikę danego typu produkcji oraz danego przedsiębiorstwa. Może zatem lepiej z góry założyć, że żaden standard (nawet dalece parametryzowany) nie będzie optymalny, a co za tym idzie ważniejsza jest możliwość tworzenia w systemie MES własnych rozwiązań planistycznych bez podejmowania ryzykownych prób zawarcia w/w kompromisów.
